Sample of our inspection report form for a Reach Stacker
When you have a used reach-stacker inspected by Mevas, you will receive a 60-point checklist for the container handler. The inspector checks each point and assesses the condition.
- Basic Machine information and configuration
- Operator Station details and condition
- Engine condition and operation
- Condition of Exterior (frames, boom, sheet metal, paint)
- Visual condition of the Power Train (axles, gearbox, transmission, differentials)
- Condition of the Hydraulic system (hoses, cylinders, pumps)
- Functional test including load limitation test
- Condition of the attachment, spreader and clamps
- Comments and recommendation for repairs
- Transport dimensions
See a sample of a report below. On request we can send a PDF-version of such a report.
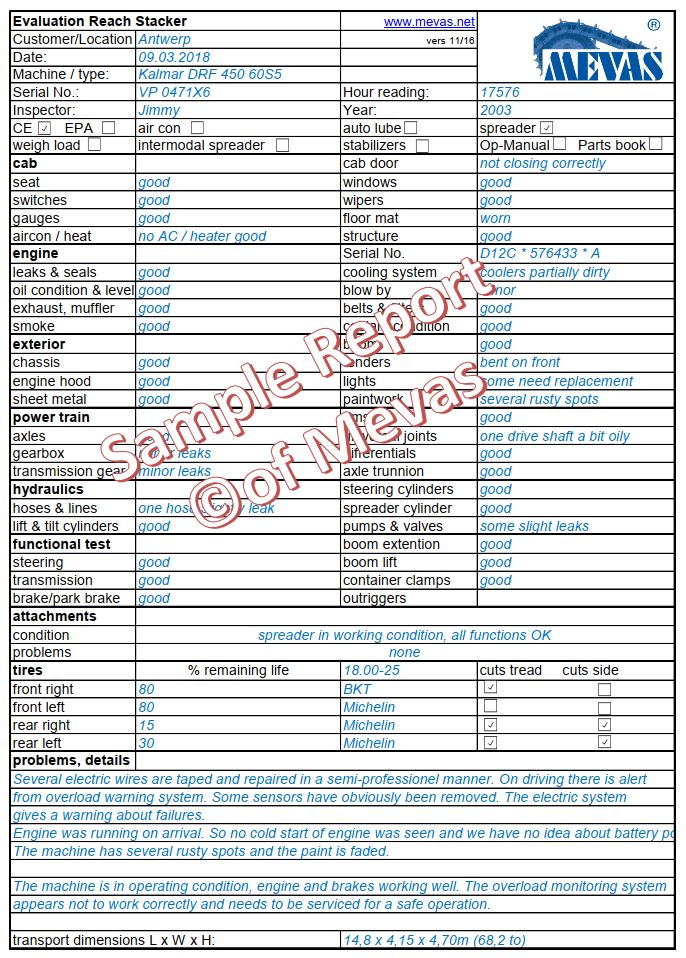
This is an obsolete sample. Our current checklist has been improved!
What extras can you order?
Once you receive an offer it will be always for a basic walk-around with functional check. This level is called TA1. On our Checklist-Options page you can find additional services which you can order.
If you have questions about the service please contact the team by Whatsapp or by phone +493520639150. We are happy to answer in detail.
Pictures and video coming with a Mevas-Report
Each machine inspection comes along with 50-80 pictures and in some cases with a short video. In case of interest it is possible to see a material handler report in detail on our Google-Drive folder.
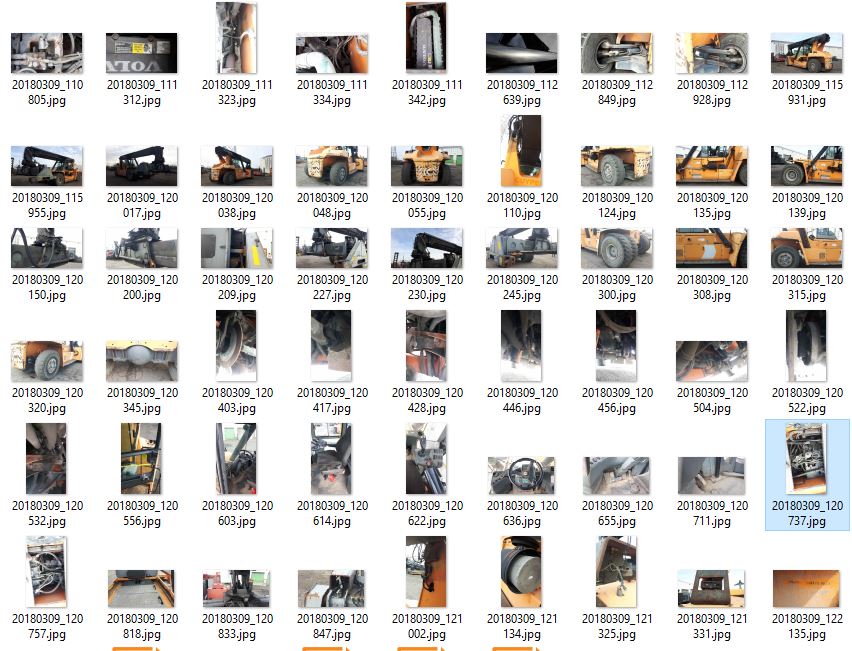
Other sample reports heavy machinery
Visit our overview for other sample inspection checklists for heavy machinery.
Keep in mind: Report forms are our legal property and copying is a violation of our copyright.
What are the most important points to check when inspecting a used reach stacker?
Inspecting a used reach stacker (like those used in container yards or heavy-duty logistics) is crucial to ensure safety, efficiency, and value. Here’s a breakdown of the most important points to check during an inspection:
🔧 Mechanical & Structural Condition
- Boom/Arm Condition:
- Look for cracks, bends, or weld repairs on the telescopic boom.
- Check for smooth extension and retraction without jerking.
- Twistlock/Spreader:
- Ensure the twistlocks are engaging and disengaging properly.
- Check for wear, damage, or misalignment in the spreader.
- Chassis and Frame:
- Inspect for cracks, corrosion, or signs of previous heavy impacts or repairs.
- Look at the rear counterweight for integrity and mounting condition.
⚙️ Hydraulics
- Cylinders and Hoses:
- Check for leaks, scuffs, or dry/cracked hoses.
- Inspect the condition of hydraulic cylinder rods and seals.
- Hydraulic Function:
- Operate all hydraulic functions (lifting, telescoping, tilting) under load if possible.
- Watch for abnormal noises or hesitations.
🛠️ Engine & Transmission
- Engine:
- Inspect for oil leaks, coolant leaks, and excessive smoke.
- Start and run the engine—listen for knocking, rough idling, or hard starting.
- Transmission:
- Check shifting in all gears and forward/reverse engagement.
- Look for slipping, jerky shifts, or delays in movement.
🚜 Wheels, Tires & Brakes
- Tires:
- Inspect for uneven wear, sidewall damage, or chunks missing.
- Make sure tire sizes match and are appropriate for the load rating.
- Brakes:
- Test service brakes, parking brake, and emergency systems.
- Check for air leaks (if air brakes), and fluid leaks.
⚡ Electrical & Controls
- Controls:
- Test joysticks, pedals, and dashboard controls for responsiveness.
- Verify lights, alarms, horn, and backup warning systems work.
- Instrumentation:
- Ensure all gauges (fuel, temp, hydraulic pressure, etc.) are functional.
- Look for error codes or warning lights.
📜 Documentation & Compliance
- Service Records:
- Review maintenance logs and check for regular servicing intervals.
- Confirm engine hours and match with wear levels.
- Load Chart & Certification:
- Verify the load chart is available and legible.
- Check for inspection certificates or regulatory compliance stickers.
👀 General Observations
- Operational Test:
- If possible, lift and move a load to observe real performance.
- Check for smoothness, noise, and vibration.
- Operator Cab:
- Evaluate visibility, seat condition, mirrors, and safety equipment.
- Make sure the air conditioning/heating and wipers function if applicable.
If you’re serious about buying, it might also be smart to bring in a MEVAS heavy equipment mechanic for a full diagnostic.
What is a Reach Stacker and what are the key features?
A Reach Stacker is a type of heavy-duty vehicle used primarily in ports, container terminals, rail yards, and logistics hubs to handle intermodal containers. It’s designed to lift, move, stack, and transport containers over short distances with speed and flexibility.
🏗️ What is a Reach Stacker?
- It’s similar to a forklift but far more powerful and specialized.
- Uses a telescopic boom with a spreader on the end to handle standard ISO containers (20ft, 40ft, etc.).
- Can stack containers typically up to 5-high and 3-rows deep, depending on model and capacity.
- Offers better maneuverability and faster cycle times than traditional container handlers like top loaders.
⭐ Key Features of a Reach Stacker
1. Telescopic Boom (Arm)
- Extends and retracts to place containers at various depths and heights.
- Provides reach capabilities to access containers in the second or third row without moving others.
2. Spreader Attachment
- Equipped with twistlocks to securely grip containers.
- Can adjust to fit 20ft, 40ft, or even 45ft containers.
- Some models have rotating spreaders for more flexibility.
3. High Lifting Capacity
- Typically ranges from 30 to 45 tons for first-row lifts.
- Decreases with reach (e.g., second/third row lifting may be limited to 25-30 tons).
4. Hydraulic Systems
- Powers the lifting, tilting, and extension of the boom.
- Allows smooth, precise control for container handling.
5. Heavy-Duty Tires & Axles
- Built for rough terrain and heavy loads.
- Some models have all-wheel steering for tight spaces.
6. Operator Cab
- Elevated for clear visibility of container stacking.
- Equipped with ergonomic controls, digital displays, and sometimes climate control for comfort.
7. Stability & Safety Systems
- Counterweights balance the load.
- May include load sensors, anti-tip systems, and stability indicators.
8. Advanced Electronics (on newer models)
- Touchscreens, telematics, GPS tracking.
- Automated container recognition, or fleet management systems for large operations.
🛠️ Common Use Cases
- Stacking containers in port terminals or rail depots.
- Transloading between rail and truck.
- Container yard management, where flexibility and speed matter.
Well known brands are Kalmar, Hyster & Konecranes
A recognized seller of used Reach Stackers is Hinrichs Stapler in Germany.
Liste de contrôle pour une Chariot élévateur à mât rétractable
Tu trouveras ici un exemple de liste de contrôle pour une Chariot élévateur à mât rétractable. Cette fiche d’inspection est utilisée pour inspecter les machines d’occasion. 60 points sont contrôlés et l’inspecteur note toutes ses observations et décrit les défauts constatés. Tu trouveras une liste de tous les formulaires disponibles ICI. La version de la liste de contrôle présentée ici n’est pas la version la plus récente. Nos rapports d’inspection sont régulièrement mis à jour.