What is a CAT TA-2 inspection ?
There are different types of inspections for used Caterpillar machines. There is the TA1-level for a standard inspection and the TA2-level for inspections with more in-depth investigations.
In line with the needs of our customers, we generally offer inspections at the TA1+ level. Can you imagine what that means? It is a visual inspection that includes a performance test and a functional test. Engines, gearboxes and torques are tested by running the machine. Tyres or Undercarriage are measured and estimated for remaining life. A detailed inspection checklist is prepared and photo documentation is taken. The so-called Product Status Report PSR is downloaded from the ECMs. And we look out for weak points on the equipment. If you have questions afterwards, we are there for you and answer them quickly.
Is a CAT TA-1 inspection sufficient?
For larger machines, a TA1 inspection is often not sufficient. Machines have a service life that far exceeds that of a standard earthmover. For these machines we offer an extended inspection service similar to TA2 on request. Our engineers do filter cutting, oil sampling, opening the final drives and take cycle times. We know the required specifications for CAT-equipment. For midsize and smaller machinery a TA-1 Plus is the best solution.
By the way, the level of a CAT-TA inspection applies as well for all other brands such as Liebherr, Komatsu, Hitachi or Volvo CE. If you are looking for used heavy machinery try a search here.
Do you have any experiences with Caterpillar TA2-level inspections? Let us know in the comments below.
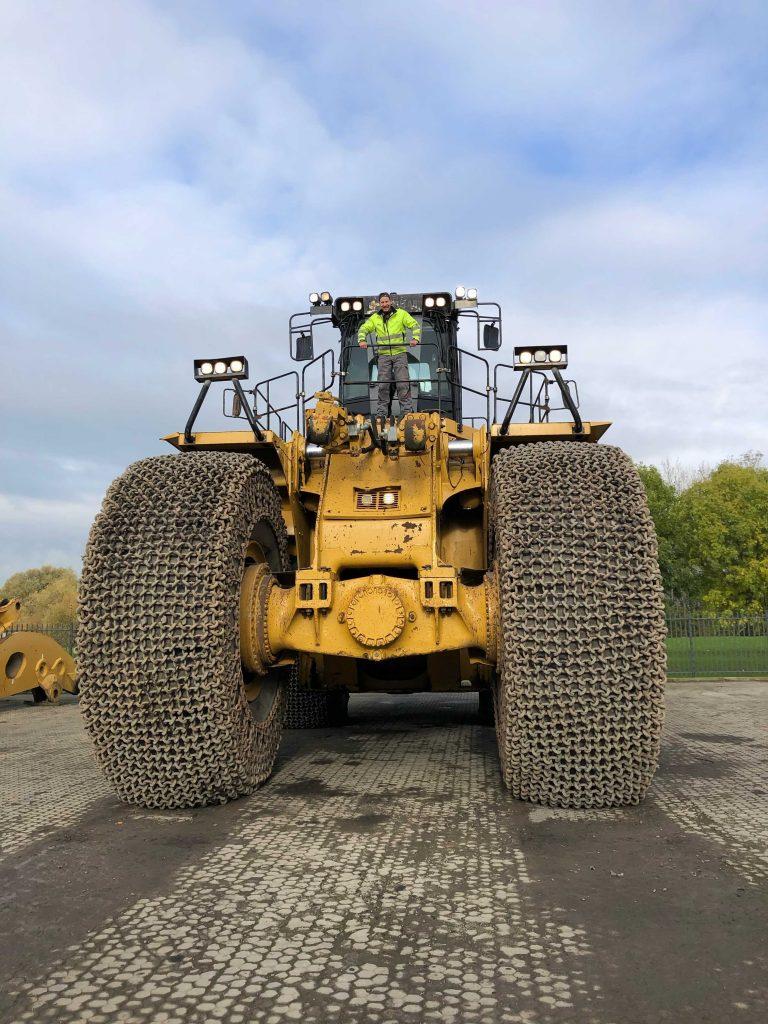
What operational testing should a detailed inspection for a used heavy machine include?
A detailed inspection for a used heavy machine should include various operational tests to assess the machine’s performance, safety, and overall condition. These tests help identify any potential issues, defects, or areas that require maintenance or repair. Here are some key operational tests that should be part of the inspection:
- Engine Performance Test:
- Start the machine and observe the engine’s startup, idle, and shutdown procedures.
- Check for abnormal noises, vibrations, or smoke emissions.
- Test engine throttle response and acceleration.
- Evaluate the machine’s ability to maintain a consistent RPM (revolutions per minute) under different loads.
- Hydraulic System Test:
- Test the hydraulic functions, such as lifting, lowering, and tilting (for equipment like excavators and loaders).
- Check for hydraulic leaks or abnormal fluid levels.
- Assess the responsiveness and smoothness of hydraulic controls.
- Transmission and Drive System Test:
- Test the forward and reverse gears (if applicable).
- Evaluate the functionality of the transmission, including smooth shifting and proper engagement.
- Inspect the performance of the differential and drive axles.
- Brake and Steering System Test:
- Check the braking system for responsiveness and effectiveness.
- Test the parking brake and ensure it holds the machine securely.
- Assess the steering system for smooth operation and proper alignment.
- Electrical System Test:
- Check the operation of all electrical components, including lights, indicators, gauges, and warning systems.
- Test the battery, alternator, and starter to ensure proper charging and cranking.
- Attachments and Accessories Test:
- If the machine has attachments or accessories (e.g., buckets, forks, blades), test their functionality and alignment.
- Check for wear and tear on the attachment points and pins.
- Operational Efficiency Test:
- Evaluate the machine’s overall efficiency in performing its intended tasks. This can include lifting capacity, digging power, or other relevant factors based on the machine’s type and purpose.
- Safety Systems Test:
- Test safety features such as seatbelts, rollover protection systems (ROPS), and other safety interlocks.
- Ensure that warning signals and indicators work properly.
- Noise and Vibration Assessment:
- Listen for unusual noises during operation that may indicate mechanical issues.
- Assess the level of vibration and its impact on the operator and machine components.
- Load and Performance Tests:
- For specific heavy machinery, conduct load tests to assess their performance under load conditions.
- Check for stability, tipping, or structural issues when handling loads.
- Functional Test of Special Features:
- If the machine has specialized features (e.g., GPS systems, advanced control systems), ensure they function as intended.
- Safety Inspections:
- Verify that safety guards, shields, and other safety features are in place and functional.
- Ensure all emergency shut-off systems are operational.
A detailed inspection may also involve using diagnostic tools and equipment to assess the machine’s performance and condition more accurately. It’s important to document the results of these operational tests in a comprehensive inspection report, which can help potential buyers or users make informed decisions about the machine’s purchase or use. Additionally, consulting the manufacturer’s guidelines and specifications for the specific machine being inspected is advisable to ensure that all relevant tests are performed.